
无锡新光粉体科技有限公司
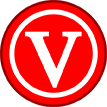
已认证
无锡新光粉体科技有限公司
已认证
燃料电池发电原理是将氢气和氧气的化学能 经电化学反应方式产生电能,氢气在阳极解离为 H+,通过质子交换膜后,在阴极与氧气反应生成水,电子从阳极通过外电路到达阴极,在外电路上形成电流回路。这种方式不受卡诺循环限制,由于其能量转化率高 40%~60%,并且具有清洁、无污染、无噪声、无红外等特点,被认为是21世纪首选的高效、洁净的发电技术,同时也是一种理想的移动电源技术,可被广泛应用于汽车交 通、军事备用电源、水下航潜器等诸多领域。
双极板作为燃料电池的关键组件之一,占据燃料电池电堆重量的80%和成本的45%,其主要作用是分配反应物气体、输运反应物产物、收集并传导电流、支撑膜电极、传递多余热量等。因此,双极板需要具备如下性能要求:
1)为保证多余热量的散出,电池温度分布均匀,极板材料必须是良好的导热材料;
2)为减少热量的产生,提高电池发电效率, 极板材料需具备较高的导电率,同时极板面接触电阻需尽可能小;
3)氢气和氧气不能混合,要求极板必须严格分离阴阳极反应物的特性,具有良好的阻气性;
4)双极板起到向阴极提供氧化剂和向阳极提供还原剂的作用,要求反应物能够顺利地通过极板表面且供给均匀分配,反应产物能够通畅排出避免造成堵塞水淹等不良现象;
5)质子交换膜呈酸性电解质,极板始终与膜电极紧密接触,为此要求双极板在酸性条件具备良好的化学稳定性,不会在工作电位和温度下发生化学分解和严重腐蚀;
6)极板材料应具备良好的加工性和一定的机械强度,极板表面的槽道已成型且在一定装配压力下不易损坏;
7)极板材料应尽可能纯净,不含有易分解易分散物质,特别是不含使质子交换膜中毒的成分;
8)极板要有较好的机械强度,保证薄型双极板满足相关使用条件,符合机械振动要求,提升电池体积功率密度;
9)尽量选择密度较小材料,提高电池重量功率密度;
10)要求双极板加工周期要求,降低双极板 生产加工成本。对此,美国能源部对燃料电池双极板材料提出了具体要求如表1所示。
目前燃料电池双极板主要使用材料包括四种:传统人造石墨双极板、金属表面改性双极板、复合材料双极板和柔性膨胀石墨双极板。
其中人造石墨双极板是最常用的极板材料,生产技术难度低,采用无孔石墨进行机械加工雕刻,导电性、导热性、耐腐蚀性和气密性各方面都比较优异,但是加工时间成本太高,大批量生产效率太低;
金属双极板具有易成型、极板轻薄、体积功率和重量功率密度高等优点,但是在含氧且酸性环境中面临严峻的腐蚀问题和接触问题,表面改性可提高使用寿命,成本增加;
复合材料双极板加工简单,成本较低,但是在导电性能和气密性方面两者很难平衡,以至于至今应用不够广泛;
柔性膨胀石墨双极板由天然鳞片石墨经氧化插层、高温膨胀后压制而成,加工简单,可大规模批量生产,具有耐腐蚀、良好导电导热、阻气隔气等特点,集成了传统石墨和金属材料极板的优点,是一种较为理想的双极板材料,也已在燃料电池市场成功应用。
1 膨胀石墨在双极板研究现状
柔性膨胀石墨双极板是一种以可膨胀石墨为基材并辅以材料复合改性的双极板,属于复合材料双极板类型中衍生出的一种具有广泛应用潜力的类型,众多学者在该领域做了相关研究,其制备路线大致可以分为直接模压和预制板模压两种。
1.1 直接模压膨胀石墨
直接模压膨胀石墨双极板材料是由膨胀石 墨、聚合物固化树脂、辅助导电材料均匀充分混合后模压成型,之后还需进行固化处理。使用膨胀石墨直接模压成型与传统的石墨和人造石墨相比,不需要额外的二次石墨化处理,且柔性的膨胀石墨具有良好的压制成型性能。但也存在极板强度不足和隔气不良等问题,为此需要在压制过程中添加额外的聚合树脂与之混合,增强极板强度和改善极板气密性能。为此存在一个配比问题, 高导电率要求极板材料混合膨胀石墨成分多些,而高气密性和高强度需要混合树脂含量多些,这样就构成了膨胀石墨双极板材料成分的一对矛盾体。
为解决这个矛盾,同济大学史惟澄等人使用导电填料来增强双极板的电导率和机械强度,树脂可选择的种类如聚丙烯、聚偏氟乙烯、聚苯硫醚、乙烯基醋树脂和环氧树脂等;辅助导电填料材料可选择碳纤维、碳纳米管、石墨烯等,制备了性能符合要求的膨胀石墨双极板。
湖南大学刘洪波教授以膨胀石墨为导电骨料、炭黑为添加剂、酚醛树脂为黏结剂,采用湿法直接模压成形工艺制备质子交换膜燃料电池用膨胀石墨/酚醛树脂复合材料双极板。同时还考察了树脂含量、成形压力、添加剂用量及添加剂加入方式对复合材料双极板性能的影响。研究结果显示双极板机械性能和气密性能满足使用要求。
此外,广东工业大学宋丽娜、华东理工大学常丰瑞都先后采用预先混合直接模压的工艺制备膨胀石墨双极板,达到比较理想的测试性能。
1.2 预制板压制膨胀石墨
预压板模压制备双极板是以膨胀石墨为基础材料,通过滚压预制成低密度柔性石墨板,再通过真空模压成高密度的柔性双极板。这种方法利用了膨胀石墨连续的石墨相,因此可以制备出导电性能优越的极板。
中科院大连化物所罗晓宽采用的技术工艺 路线是:先将膨胀石墨压制成低密度柔性板,再将柔性石墨板仿真灌内进行聚合物树脂真空注胶处理,随后进行压制成型具有流道的单极板,最红经过烘箱固化成满足实际环境条件应用的聚合物/膨胀石墨双极板。通过这种方法制备的双极板,依然保持了膨胀石墨内部连续的相间结构,有着优越的导电性能,同时具有良好的挠曲性能。
此后,大连化物所杜超采用真空浸渍结合模压的方法,选取乙烯基酯树脂(VE)和膨胀石墨(EG)板材为原料制备复合双极板,制备了一系列树脂含量均为14%的复合材料,同时作者还考察了微观结构以及成型压力对双极板材料的导电性能、密封性能、机械性能以及表面亲/憎水性的影响,并通过实际电池性能验证了极板的稳定性及可靠性。
国外在膨胀石墨极板方面有着较为成熟的技术和丰富的生产经验。作为燃料电池龙头企业Ballard公司,一直采用以膨胀石墨作为双极板材料,通过数十年的工艺摸索,成功开发出性能稳定可靠且寿命长久的柔性石墨双极板,并将其应用各种型号的质子交换膜燃料电池电堆中。
其制备过程与大连化物所不同,先将膨胀石墨滚压成低密度柔性板,再通过压机压成型高密度极板,后续再进行聚合物真空浸渍、烘箱固化等处理, 最终制备了性能优异的膨胀石墨双极板。从目前市场使用情况来看,Ballard膨胀石墨极板在市场已累积运行超过2万小时,性能依旧平稳,表现出十分优异的性能,完全满足工程使用要求。
目前国内广东氢能国鸿公司已将此技术引进并吸收,形成规模化、自动化生产。此外,国外如日本日清纺株式会社、美国大型石墨制品公司 Graf-tech、加拿大大型石墨制品公司Zenytta都相继研发了膨胀石墨双极板及生产线,并都与Ballard动力公司展开过合作和研究。足以说明,膨胀石墨已经得到国内外燃料电池行业以及市场的高度重视,具有巨大应用潜力。
2 膨胀石墨双极板制备工艺流程
常用的膨胀石墨双极板制备过程包含以下几个步骤:天然石墨材料膨化处理、柔性石墨板制备、模压柔性石墨板制备单极板、真空浸渍树脂处理、热压整平极板、丝网印刷涂胶、双极板粘接处理、极板切边。其中柔性石墨板的制备、真空压制、浸渍处理是整个制备过程核心。
2.1 膨胀石墨板制备过程
膨胀石墨板的制备直接影响双极板各项指标性能,是双极板制备的关键步骤。通常采用天然鳞片石墨材料制备,通过强酸氧化在石墨层间形成化合物,保留石墨原有连续相的结构基础上增加了石墨层间距离,改变原有石墨的某些特性,形成一种具有优良柔软性和回弹性的物质,达到极板材料的使用要求。最终制备的膨胀石墨形状像蠕虫,所以也叫做石墨蠕虫,如图2所示。
制备膨胀石墨的关键在于层间化合物的生 成,而在天然鳞片石墨在化学氧化过程中,石墨边缘区域和层间区域是同时进行的,倘若石墨纯度不够,则会因杂质的存在而引起石墨晶格缺陷和位错等的情况出现,使石墨层状晶格遭到破坏,同时影响膨胀石墨的导电性能。为此在制备前期,需要将原料中多余的矿物质剔除,保证足够的纯度。
一般燃料电池用膨胀石墨的生产工艺流程如图3所示,天然鳞片石墨材料粒度需要经过一定的筛选。
石墨粒度对膨胀石墨性能影响很大,不同粒 度的石墨膨胀后所具有的比表面不同,石墨的膨胀厚度以及层间深度都不一样,所表现出来的特性差异较大。一般石墨粒度太大,表现出层间化合物形成不够充分;石墨粒度过小将会导致石墨边缘氧化过快,不利于层间化合物的形成,经过筛选的石墨粒度目数通常在80~200目左右。随后对所筛选的石墨进行提纯处理,通常要求纯度达到99.9%以上,保证具有良好的导电性能。
在将插层剂与鳞片石墨按比例混合均匀且反应充分,通过插层剂控制层间化合物的生成,减少边缘化合物的生成,进而达到膨胀作用。常用的插层剂有硝酸、硫酸、高锰酸钾等。待石墨氧化反应充分后,经过脱酸、水洗、干燥等工序,将残余的插层剂去除干净,同时添加相应的抗氧化剂,防止石墨在高温条件下氧化。将干燥后的石墨放置 800~1200℃下进行高温膨化,使石墨层间化合物快速分解,并利用分解产生的推力将层间距拉大,最终形状蠕虫状的石墨条,长度可达1~2 cm。
在此过程既要控制膨化的温度,又要掌控好膨化时间,时间过长容易造成石墨粉碎性破裂,时间过短层间化合物分解不完全,膨胀程度不够;温度过高容易造成石墨氧化,温度过低分解速度太慢。因此需要认真研究石墨膨胀过程温度、湿度、时间、等工艺参数与产品性能的关系,确保能够 生产性能稳定的膨胀石墨。膨胀石墨在压制和滚压的过程,蠕虫状膨胀石墨条相互啮合,形成具有柔性强度的低密度板材,这种板材内部依旧保持石墨相连续结构,具备优越导电性能。
2.2 真空压制
将低密度柔性石墨板压制成高密度板,并印 上相应的流道结构,这是压制成型的主要内容。柔性石墨在低密度状态呈蓬松状态,内部存在很多间隙的空洞且充满了气体。在压制的过程中,为了尽可能减少因内部气体聚集而造成的鼓包现象,应尽可能在真空状态下进行压制成型。柔性石墨极板模压制备工艺流程如图4所示:
为实现真空压制,需要设计专用真空模压装置,如图5所示。设计压机的上座和围裙构成一体,在压机上座和下座上安装相应的压制模具,在模具之间放置低密度柔性石墨板;上座围裙下降至密封位置时,可由上座、下座和密封结构组成密封腔室,从底座孔洞抽取真空外连接真空泵,整个压制模具在真空环境中。
当真空要求达到设定值时,停止抽真空,进行合模压制并按工艺要求进行保压;撤除密闭空腔真空要求,注入氮气,撤回上座模具,取出压制样件。在真空状态压制,可以有效的降低极板表面鼓泡风险的存在。
2.3 浸渍改性处理
通常柔性石墨板的密度与石墨板透气性能密切相关。随着密度的增加,石墨透气系数逐渐减小,板子的气密性能变好,期间起决定影响的是内部空洞的影响所致。对于封闭的空洞,成型压力的增加仅仅增大了板子的密度,减小空洞的空间大小,并不会对透气造成负面影响,真正受影响的是半封闭空洞。
当柔性石墨板密度很低时,板材内部存在着大量的半封闭孔洞,甚至存在一些很大的空洞,在表面也可以发现很多的孔隙,甚至是小的裂缝,用手撕开表面后可直接看到层的结构,内部有较大的孔洞存在,说明低密度板材在气密性方面存在较大的缺陷。当成型压力达到100 MPa 时,柔性石墨板密度可达1.5 g/cm3甚至更高,利用扫面电镜可观察到表面结构和揭开后的层状结构,发现其表面比较平滑,只有很小的缝隙,半封闭孔明显减少,气密性得到明显改善。
尽管如此,在其内部仍然存在各种细微孔隙,这些孔隙仍然直接影响板子的气密性;另一方面,紧靠蠕虫石墨之间的相互咬合难以承受结构的抗弯强度,很容易导致裂纹、撕毁和破坏性的损坏。为此,需要比采用浸渍注胶的工艺改善极板的密封性能和机械性能。
详细的柔性双极板注胶工艺流程如图6所示,将已成型的柔性双极板放置真空浸渍灌中,同时按比例配制好需要浸渍注胶的树脂溶液;进行真空抽取,待罐内压力达到设定值后停止抽真空并开启浸渍液阀门,达到设定液位关闭输液阀门,同时进行加压浸渍,压力设定在1.5 MPa左右。浸渍时间由浸渍剂类型而定,待浸渍完成后,将压力降至 2.0 bar,开始回液阀门将浸渍液压回储液罐。紧接对石墨板进行清洗、烘干及固化处 理。
3 后续需要研究解决的问题
虽然膨胀石墨在燃料电池领域已有成功应用的案例,但是不管是直接模压还是预压成型后注胶制备膨胀石墨双极板,期间还是存在一些技术难题:
1)通过直接模压制备膨胀石墨双极板,膨胀石墨与树脂的混合是模压成型工艺中最重要的环节。传统的干混是将膨化的蠕虫石墨与树脂颗粒通过螺杆挤压或者三维立体摇匀机混合均匀,但仍然会出现树脂颗粒局部集中的现象,因为树脂颗粒密度远大于膨胀石墨粉。
后来又有很多研究人员采用研磨的方法将树脂和石墨充分混合,但是这种方法是通过剪切力破坏膨胀石墨的蓬松结 构,以至于石墨蠕虫粉碎,从而失去了膨胀石墨的使用价值。因此,需要寻找一种不破坏膨胀石墨结构且能够与树脂材料均匀分布的混合方式,同时还可以在混合过程中添加密度与膨胀石墨相近的辅助填料,增强材料的导电性能。
2)天然石墨由六角形阵列或碳原子网络的层面组成。这些六边形排列的碳原子层平面基本上是平坦的,并且是定向和有序平行排列,且彼此等距。通常基面基本是平坦的,平行等距的碳原子片层或碳层被连接或结合在一起,并且其基团排列在微晶中。高度有序的石墨由相当大的微晶组成:微晶相互高度排列或取向,并具有良好的有序碳层。这种高度有序的石墨导致高度优选的微晶取向,因此表现出或具有很高的定向性,例如导热性和导电性以及气流体扩散性在不同方向差异较大。
简而言之,石墨的叠层结构,即由较弱的范德华力连接在一起的碳原子叠置成层,在平面方向和垂直板平面方向性能差异巨大。为解决这一问题,需要在预制膨胀的过程添加相应的辅助剂料,来改变膨胀石墨蠕虫的有序结构,增强板材竖直方向的导电性能和导热性。
来源:船电技术 作者:花仕洋 徐增师 余罡 彭恩高
(武汉船用电力推进装置研究所)
免责声明:本文系网络转载,版权归原作者所有。如涉及作品版权问题,请与我们联系,我们将根据您提供的版权证明材料确认版权并按国家标准支付稿酬或删除内容!本文内容为原作者观点,并不代表本公众号赞同其观点和对其真实性负责。
相关产品
更多
相关文章
更多
技术文章
2020-09-03技术文章
2020-08-14技术文章
2020-07-27技术文章
2020-07-21