
元能科技(厦门)有限公司
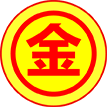
已认证
元能科技(厦门)有限公司
已认证
随着锂离子电池产业的高速发展,人们对电池使用过程中的安全性和稳定性的关注日益增多,锂离子电池的性能衰减主要原因可以概括为活性锂损失、活性材料损失、极化损失等;在实际锂离子电池开发中,从原材料到电极制备及成品电芯组装,各层级的特性及其演化均会影响到电池的性能。因此, 在锂离子电池的研究工作中,建立从粉体材料到极片再到电池的多层级关联性是十分重要的,也是当前锂电研究者关注的重点。
元能作为一家设备自研公司,除了关注设备本身的性能之外,更致力于寻求机理分析方法上的突破。在前期的工作中,曾自主设计实验,选用5个不同电阻率的三元粉末,固定53.3%的固含量,按照质量比例96.5:1.5:2(活性物质:导电炭:PVDF)进行浆料制作,并完成系统化涂布、辊压、冲片、扣电组装,分别结合粉体、浆料、极片、扣电导电性能变化分析各层级关联性,图1为各层级关联性示意图。测试结果显示从粉末层级到浆料层级,由于制备浆料时加入了其他辅料和溶剂,再加上制备工艺的波动性,导电性趋势未表现出完全一致的状态;而到扣电层级的直流内阻,由于各扣电组件的电子电阻、电荷转移电阻及锂离子扩散电阻等的影响,层级关联性也存在不一致的现象,但对于粉体层级差异比较大的1号和5号材料,各层级的关联性还是比较一致。
图1.锂电不同层级关联性分析
从粉末到混合粉末预混,到浆料,再到电极层级,微观组成与结构处于不同形态,如图2所示。对于粉末层级的电导率,由于仅包含活性颗粒,一定压实状态下电导率可表达为:σAM =σ0*φ/τ,其中σ0*为粉末本身的电导率,φ为压实状态下粉末颗粒的体积分数,τ为粉末颗粒连通的迂曲度,与颗粒之间的接触状态相关,连通性越好、接触面积越大,τ越小。粉末电导率测试过程中,随着压力增加,压实密度增加,颗粒体积分数φ增加,颗粒之间的连通性和接触更好,τ变小,因此粉末电导率升高。
而从混合粉末预混态到浆料,再到电极,向活性颗粒粉末中引入了导电剂和粘结剂。导电剂有利于电子传输网络的构建,而粘结剂会增加电子传输阻抗。混合粉末或浆料或电极涂层的电导率可以分为两个部分:活性颗粒相互连通形成的导电网络和导电剂形成的导电网络,当然两者之间的接触也能形成电子传输网络。此时,有效电导率可表达为:
其中,σeffe为有效电导率;φact为活性颗粒粉末的体积分数;τact为活性颗粒粉末的连通迂曲度,连通性越好、接触面积越大,电子传导路径的迂曲度τ越小;σact为活性颗粒本身的电子电导率。φsub为导电剂粉末的体积分数,τsub为导电剂粉末的连通迂曲度,σsub为导电剂颗粒本身的电子电导率。一般地,活性颗粒的本身电导率远低于导电剂,特别是正极。因而活性颗粒贡献的电子电导率很小,导电剂是电子传导的主要路径,因此导电剂的分布状态与连通性是影响电子电导率的主要因素。与纯粉末相比,浆料到电极中导电剂和黏结剂的引入,直接影响电子导电性能的评估结果。从混合粉末预混态到浆料,再到电极,电子导电率的关联性主要与组分的分布状态和连通性相关,特别是导电剂的连通网络,如果这种导电网络能够在工艺过程中一直保留下来,则各层级电导率会完全相关。
图2.各层级颗粒微观形貌
从原材料到器件各层级关联性是锂电领域的一个庞大课题。从另一个维度思考,大家最终的关注点一直是最终端电芯的性能,但在当前状态下,各层级质量严控是关键,但如果能提前一个层级明确问题根源,提前预估问题也可进一步避免时间和成本的大量浪费。元能一直以来也接收到合作客户层级关联性的需求,尤其是粉体电阻及压实密度与极片电阻及压实密度的关联性,实验室机理端探索过程也尝试多种方法去寻求关联性的突破,本篇文章旨在结合已经做的一些探索性工作做下思路行分享。
2. 锂电粉体预混状态电阻率关联极片层级电阻率
不同层级关联性(图1)的探索工作中发现,粉体层级与极片层级的关联新不一致(导电剂的影响显著),但浆料到极片的关联性完全一致,主要考虑的还是粉体到浆料到极片过程,导电剂,黏结剂的引入,直接影响电子导电性能的评估,为进一步明确影响,实验室设计以NCM材料为主,参考干法搅拌工艺中的预混部分,分别按照NCM:PVDF=19:1及NCM:PVDF:SP=18:1:1配比充分混合制备不同配比的混合粉体,并结合PRCD系列设备对不同混合的粉体进行电阻率评估测试,进一步明确粉体混合前后导电性能差异。如表1为粉体预混前后电阻率测定的结果差异,从结果上看,在NCM中掺混PVDF后,由于粉体状的PVDF导电性较差,混粉后的样品相比纯NCM粉体表现出导电性变差的现象,而同时掺混导电性较好的SP后,混粉的导电性能得到有效提升,进一步明确相对于粉体材料,正极极片层级导电性的提升主要归功于导电剂的引入。在粉体层级电阻率和极片层级电阻率的关联性探究中,通过粉体预混状态的电阻率进行关联是一种可尝试的思路,当前元能已经逐步在完善自有的扣电线,下一阶段将结合自有搅桨、涂布、辊压工序进一步明确该思路的可行性。
表1.粉体预混前后电阻率测定差异
3. 锂电极片电阻率与涂覆层粉体电阻率关联性探究
预混粉体的实验中,大家可能会关注到一个点,极片层级导电剂和黏结剂的引入状态与纯粉体预混是有明确差异的,经过浆料层级时的搅拌,PVDF已经是溶胶状态的存在,还有溶剂的引入,在极片层级烘干后的状态与预混也是有明确差异的,关于这一点元能的小伙伴们同样也提出了质疑,于是同步设计了极片层级刮粉,针对极片刮粉后粉碎的粉体状态进行电阻率测试,结合BER及PRCD系列设备评估其与极片层级电阻率的关联性。
在这一部分实验中,分别选取NCM和LCO两种未辊压的极片作为样品,并对样品进行25MPa压强下不同位点电阻率的测试,以明确选取极片的涂覆均匀度合理,避免变压测试阶段引入各位点差异过大。如图3为BER系列设备原理图及所选取极片的单点测试结果,分别选取极片不同位置的6个点,计算其电阻率变异系数COV,从结果上看所选极片的COV均小于5%的水平,初步明确所选极片的均匀性良好,可作为本实验评估的样品极片。
图3.BER系列设备原理图及极片单点测定结果
按照实验设计思路,分别对两种极片进行刮粉处理,刮取集流体表面的涂覆层粉体,并对刮下的粉体进行研碎处理,以确保粉体端电阻率测定过程的取样均匀性。如图4为PRCD系列设备原理图及极片涂覆层粉体电阻率测定结果,从曲线上看,涂覆层粉体表现出与纯粉体相同的趋势,均随着压强的增大,电阻率逐渐降低。为进一步明确差异,结合极片电阻率和涂覆层粉体电阻率的结果进行对比分析,表2为实测结果对比表,从结果上看两者数据未呈现数量级上的差异,且从两种类别的电阻率差异上看,LCO两种状态下的电阻率均大于NCM,初步看来该思路是合理有效的。由于样品选取的局限,当前实验验证仍不够系统,需进一步设计同一主材类别的不同工艺条件的实验进行验证,同时也在考虑除了刮取涂覆层粉体进行对比验证外,直接在浆料层级模拟涂覆状态烘干后或直接浆料烘干后进行研碎处理,以此关联极片性能,如果明确可行,是否可以在不进行涂覆的情况下完成极片层级性能的预估?下一步元能内部也需进一步设计实验逐一明确。
图4.PRCD系列设备原理图及极片涂覆层粉体电阻率测定结果
表2.极片电阻率与涂覆层粉体电阻率对比表
4. 小结
伴随行业发展的增速,锂电各层级间的关联性一直是大家关注重点,其中材料导电性能与电芯电性能、安全性能评估息息相关,本文结合实验室的测试经验,为粉体电阻率和极片电阻率的相关性提供了一些新的思路。实验通过粉体层级的预混及测试评估,明确黏结剂、导电剂引入对电阻率的直观影响,此外考虑到溶剂的引入影响及黏结剂状态的差异,对成品极片刮取涂覆层粉体进行了对比测试,初步评测可以作为一种有效思路进行关联性探究,下一步元能也将细化试验方案,推动更加系统化的关联性评估。
5. 参考文献
【1】杨绍斌, 梁正. 锂离子电池制造工艺原理与应用.
【2】mikoWoo@理想生活.锂离子电池极片理论及工艺基础.
相关产品
更多
相关文章
更多
技术文章
2025-02-20技术文章
2025-02-13技术文章
2025-01-14技术文章
2025-01-09虚拟号将在 秒后失效
使用微信扫码拨号