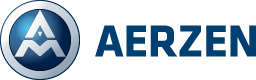
艾珍机械设备制造(上海)有限公司
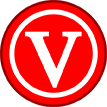
已认证
艾珍机械设备制造(上海)有限公司
已认证
In pneumatic applications or in municipal and industrial waste water treatment, the generation of process air is very energy-intensive. When operators use the right compressor for their process, they save energy. The extensive Delta Hybrid rotary lobe compressor series has therefore been further developed, optimised and supplemented by three sizes.
Since
its successful introduction in 2010, the Delta Hybrid rotary lobe
compressor series has been continuously expanded. With all in all 18
sizes the Delta Hybrid now cover volume flows of 110 m³/h up to 9.000
m³/h and drive power from 5.5 kW to 400 kW. The new Delta Hybrid D76S
with a maximum volume flow of 4,580 m³/h and a drive power of 160 kW
closes the gap in the upper power range. In the low volume flow rate
range, two further sizes complete the portfolio for an even finer
gradation of the series. In addition to the new D19S with a maximum of
1140 m³/h and 45 kW, the new size D29S with a maximum of 1740 m³/h and
75 kW also joins the product range. D76S, D29S and D19S operate in the
standard pressure range.
The models D76H and D76E were developed for an increased pressure range of 1.5 bar and the vacuum range to -700 mbar.
Plant
manufacturers and operators not only benefit from the now finer tuning
and the resulting better price/performance ratio, the entire series has
also been further developed and optimised. In this way, further
efficiency potentials could be tapped, leading to increased energy
efficiency of up to 5% per size.
AERZEN produces the optimised
series or the new models in series from the middle of the year. At the
same time, the further developed Delta Hybrid series will be equipped
with the innovative AERtronic machine control system for process
monitoring and control. With the new machine control the series of
AERZEN rotary lobe compressors has, depending on the version, a cloud
interface, automatic emergency shutdown, a digital control instrument
and a fault indicator.
Significantly improved energy-efficiency by energy savings of up to 20 % compared to conventional units;
Extended fields of application with differential pressures of 1,500 mbar in the overpressure and -700 mbar in negative pressure;
Low maintenance- and service costs (operation from the front, oil level check from the outside even with the machine in operation, oil change intervals prolonged to 16,000 operating hours), reliability and durability;
Very high regulating range (25 – 100%) with best possible degrees of efficiency also in partial load operation;
Patented and robust bearing design
Low compressed air discharge temperature thanks to excellent thermal budgets;
Compact design and side-by-side installation, low noise levels, suitable for outdoor installation.
ATEX certification as well as class 0 certification acc. to ISO 8573 for oil-free operation
No use of absorption material in discharge silencer, consequently no contamination of downstream systems;
Belt drive for ideal design of the volume flow (automatic belt tension by hinged motor mounting plate ensures low maintenance and high reliability);
Tailor-made solutions through modular construction system, various modifications and options
最新动态
更多
虚拟号将在 秒后失效
使用微信扫码拨号