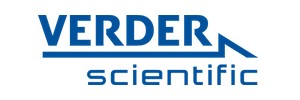
弗尔德(上海)仪器设备有限公司
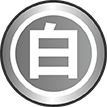
已认证
弗尔德(上海)仪器设备有限公司
已认证
锂离子电池的发展背景
从早期的锂金属阳极开始,到今天的商用锂离子电池,锂基电池技术在过去的三十年中有了显著的发展,其中的故事充满了突破性和历史进展。锂离子电池的历史可以追溯到1962年。第一批电池在单次放电后不能再充电(原电池),其负极材料为锂,正极材料为二氧化锰,由三洋公司在1972年推出。1985年,Moli能源公司开发了第一个基于锂(负极)和硫化钼(正极)的可充电电池(二次电池)。然而,由于负极上的锂,这种设计存在安全问题。通往锂离子电池的下一步是在电极的两侧涂覆上涂层,这使得锂可以储存和移除,并且具有高电压电位。索尼公司研发了第一款可充电锂离子电池,并于1991年推出,这里负极的活性物质为碳,正极的活性物质为钴酸锂。
从一开始,最具挑战性的工作之一就是选择最佳的电极化合物,特别是正极化合物。高循环稳定性和可接受的比容量的要求限制了电极材料的选择。在正极使用涂有金属氧化物颗粒的铝箔,在负极使用涂有石墨的铜箔是最常见的组合之一。图1显示了传统锂离子电池的结构,箔片可以被单面或两面涂覆。各种锂金属氧化物化合物被应用于正极,其中层状氧化物例如Li(Ni1/3Co1/3Mn1/3)O2可以获得较高的比容量。与富Ni/ co化合物相比,富Mn化合物的价格更低,因此对制造商更有利。
图1. 传统锂离子电池的结构
锂离子电池质量控制的程序之一是对电池盖、外壳、点焊处以及电极进行金相分析。由于这些部件的材料不同,所以需要不同的制备方法。本系列文章将分段讨论各种部件的制备目标和方法。
电池盖和外壳的金相制备
电池外壳作为电池系统有源和无源元件的位置,对储能系统的功能、安全性和使用寿命起着决定性的作用。它保护那些敏感的部件免受有害环境的影响,如水,湿气,或灰尘,是长期安全可靠运行的关键。由于汽车电池通常位于车厢外部,一般位于地板区域,电池外壳无可避免地暴露于极端环境影响下,例如温度、湿度、飞溅水、盐雾、灰尘或石屑等。因此,在恶劣的外部条件下,电池外壳的高机械稳定性和耐腐蚀性至关重要。
电池外壳的质量控制程序之一是金相制样和随后在光学显微镜及SEM(扫描电子显微镜)下的检查。用QATM Qcut 200 A精密切割机上的旋转夹具可以很方便地切割电池的盖帽。图2显示了如何将样品夹持在切割机中以切开电池盖并取出极芯。
图2.在旋转夹具中夹紧锂离子电池以切开盖帽并取出极芯
锂离子电池的壳体和盖帽的制备方法参见表1。在大多数情况下,电池盖是由铁素体钢制成的,带镍基涂层。在这里,适当的制备可以消除诸如倒角、错误的力和方向导致的涂层损坏、基材以及镍涂层涂抹等许多假象。表格中的制备方法是QATM根据其特定的设备和耗材开发的制备方法,保证制样后的结果更为准确。
表1. 锂离子电池盖和外壳的磨抛制备参数
电池盖和外壳的检测
用3%硝酸酒精溶液腐蚀锂离子电池盖样品得到的显微组织为带涂层的铁素体基体(图3)。有时为了测量盖帽的晶粒度,可以用Klemm I腐蚀剂进行彩色腐蚀(图4)。
图3:锂离子电池盖用3%硝酸酒精溶液腐蚀后的显微组织
图4:锂离子电池盖用KlemmI彩色腐蚀剂腐蚀后的显微组织
下图为扫描电镜下电池盖的背散射电子像。此外,使用扫描电子显微镜的EDS能谱探测器,可以测量涂层的化学成分。
图5:电池盖的背散射电子像,顶部的涂层清晰可见
QATM Qpix Inspect金相软件中的涂层厚度测量模块可以依据国际标准ISO 1463(金属和氧化物覆盖层.覆盖层厚度的测定.显微镜法)对电池盖的涂层进行精准的半自动测量(如图6所示),并以表格和线图的形式提供层厚度的统计值。
图6. 通过Qpix Inspect软件进行层厚测量,最终得到的层厚为5.1um。
进一步的质量控制可以通过测试锂离子电池盖和外壳的硬度来进行。在这个案例中,QATM的Qness60A + EVO显微硬度计被用于测试方法为HV1(维氏硬度,载荷1kg)的硬度测试,得到的结果为盖的硬度:117.3HV,外壳的硬度:210.6HV。图7显示了压痕的位置及图像。
图7.锂离子电池盖及外壳的HV1硬度测试
更多关于LIB的专业解读,请期待下期内容。
最新动态
更多
虚拟号将在 秒后失效
使用微信扫码拨号